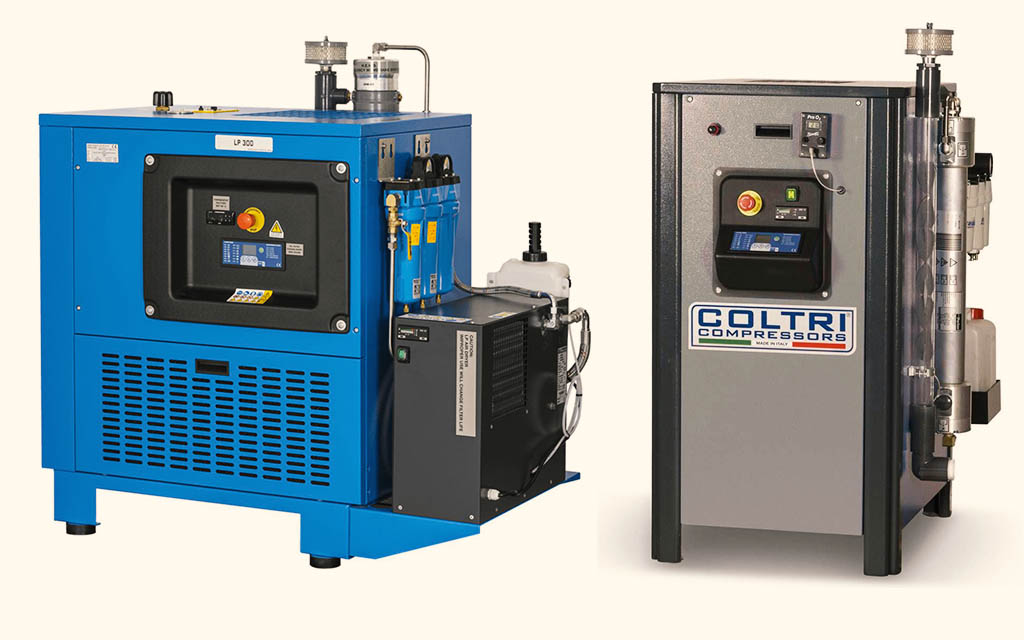
Michelle Haywood sets out the science that goes into every fill of nitrox and trimix
For many divers, especially those doing repeat dives in a day, nitrox gas is the gas of choice. Breathing a higher percentage of oxygen reduces the absorption of nitrogen into the body. This can either be used to extend no-stop dive times, or to create an extra safety margin on shorter dives.
There are two main methods used by filling stations to create the nitrox gas, either partial pressure blending or a membrane system. Partial pressure blending requires the fill technician to calculate how much pure oxygen to decant into an empty cylinder and then to top it up with air to the required percentage. In filling stations which supply trimix, the extra calculation of the helium content is also needed. Experienced gas blenders even take into account the changes in temperature as cylinders are being filled.
However, there is a simpler system which requires less maths, and that’s to use a membrane to separate some of the nitrogen out of air. As some of the nitrogen is removed, the percentage of oxygen in the remaining gas increases. Membranes are a bundle of hollow fibres and the gas from the compressor travels down the centre of the fibres.
The membrane relies upon the principle of selective permeation. Oxygen, carbon dioxide and water vapour are ‘fast’ gases in this scenario. As compressed air is fed into the membrane, the fast gases pass through the membrane and can be collected. The slow gas (nitrogen) mainly carries on through the hollow membrane fibre and is discharged. This process is governed by a number of factors, the speed of the inlet gas, the pressure difference between the inlet gas and the outlet gas, the temperature and the characteristics of the membrane itself. '
An ideal membrane would be highly selective and highly permeable to the gas you were trying to enrich (in our case oxygen). However, for most membranes, as selectivity increases, permeability decreases. Thus, a balance has to be struck. Membranes have a limited capacity and so the inlet gas is only lightly compressed (around 10-11 bar usually). If a high-pressure inlet is used, the pressure has to be regulated back to a lower level so that the membrane isn’t overwhelmed. The air is warmed to around 43ᵒC before being allowed to flow across the membrane. The gas leaving the membrane may be up to 44% oxygen and inline oxygen analysers are used to control the percentage using air to adjust as needed. More compression of the oxygen-enriched air is then required to fill a scuba cylinder.
Membrane systems are sometimes preferred by dive centres, as the requirement for training operators is less and there’s no risk from having 100% oxygen cylinders around. Also, in riskier situations such as liveaboards and some buildings, it can be hard to get insurance that covers having pure oxygen on site. Plus, it avoids the maths and the potential for errors (although there are several excellent calculation apps and tools available). Membrane filling systems tend to be slower to operate and usually dive centres will have a bank of nitrox available for decanting rather than fill direct. But if you’ve been on a liveaboard that offers membrane nitrox with limited bank capacity, then you’ll have seen how long refilling cylinders can take.
The alternative of blending gases requires a supply of pure oxygen. These cylinders of oxygen aren’t produced by any membrane technology, but by cryogenic distillation. In essence, the air is compressed a little (about 6.5 bar) and passed through a cooler to remove any water vapour. The dry air passes through a molecular sieve absorber to trap carbon dioxide, hydrocarbons and any remaining water.
Then the clean air is cooled by expansion, to the point where oxygen starts to turn into a liquid. The air stream (now part liquid and part gas) enters the bottom of the fractionating tower and as it expands slightly it cools further. The liquid oxygen falls to the bottom of the tower, and the nitrogen and argon continue to rise. A further fractionating column can be used to separate nitrogen and argon and to remove the last traces of those gases from the crude liquid oxygen. This is quite an energy intensive process, but for applications where more than 40% oxygen is required (most of the current rebreathers and anyone wanting to do accelerated decompression), the dive centre is going to need some 100% oxygen available.
Ready to start your scuba adventure? Sign up for eLearning!
You can get started straight away with the theory knowledge element of BSAC's entry-level courses, Discovery Diver and Ocean Diver, and work at your own pace using the BSAC eLearning system.
This article was originally published in SCUBA magazine, Issue 121, December 2021. For more membership benefits, visit bsac.com/benefits.
Images in this online version may have been substituted from the original images in SCUBA magazine due to usage rights.